I am Kuwabara from Dymco's reserch department.
It's October now, and I hope the typoon season is finally over here.
As opposed to my hope, the one of the biggest typhoon just hit Japan. That typoon had a strong storm that caused serious damages to our country. Moreover, another typoon is found around the very south of Japan. The route of the typoon is my huge concern.
Anyway,
Today, kindly let us intoduce our high-friction shim while we have our main product, vacuum conveyor and double press conveyor.
In more detail, this sheet is a very thin stainless sheet sprayed cermet on its surface.
In more detail, this sheet is a very thin stainless sheet sprayed cermet on its surface.
What I mean by "Spraying" is a processing method to form a film.
In more details, the fine particles of the spraying material is sprayed on its surface of our friction shim.
Using various heat source, spraying material melts or close to gets closer to a state that is almost melting.
This is how the fine particles is made.
Spraying is to add some extra functions that the base material does not originally have.
The surface of the material after spraying is extremely rough.
The suface of our product is from Ry 45 to 50μm.
The thickness around the part sprayed is 0.05m on each side, and spraying is processed on the both sides. The thickness is optional, 0.2, 0.3, 0.4, 0.5, 0.6mm. The shape and dimention is your choice, too. If you have pullies or any kind of solid part in your machine, maskig the whole oject or part of the object is an option availabe.
The tip of robot arm is one of the applications.
We, dymco, had an experiment regarding the coeffient of friction.
The coefficient of friction between the steel processed by machine and friction pad was " μ=0.3~0.35.
This is just for your reference.
In more details, the fine particles of the spraying material is sprayed on its surface of our friction shim.
Using various heat source, spraying material melts or close to gets closer to a state that is almost melting.
This is how the fine particles is made.
Spraying is to add some extra functions that the base material does not originally have.
The surface of the material after spraying is extremely rough.
The suface of our product is from Ry 45 to 50μm.
The thickness around the part sprayed is 0.05m on each side, and spraying is processed on the both sides. The thickness is optional, 0.2, 0.3, 0.4, 0.5, 0.6mm. The shape and dimention is your choice, too. If you have pullies or any kind of solid part in your machine, maskig the whole oject or part of the object is an option availabe.
The tip of robot arm is one of the applications.
We, dymco, had an experiment regarding the coeffient of friction.
The coefficient of friction between the steel processed by machine and friction pad was " μ=0.3~0.35.
This is just for your reference.
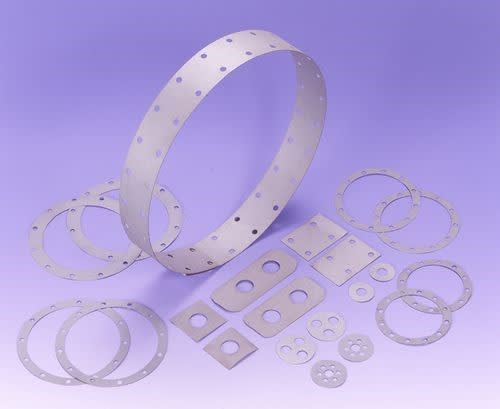
Our various high-friction sheets

This pic describes how rough the surface of friction shim is
Inquiry Form: www.steelbelt.jp/index.php#inq
Steel Belt Videos: http://www.youtube.com/results?searcmh_query=dymcooverseas&sm=12
DYMCO, LTD. URL: http://www.steelbelt.jp